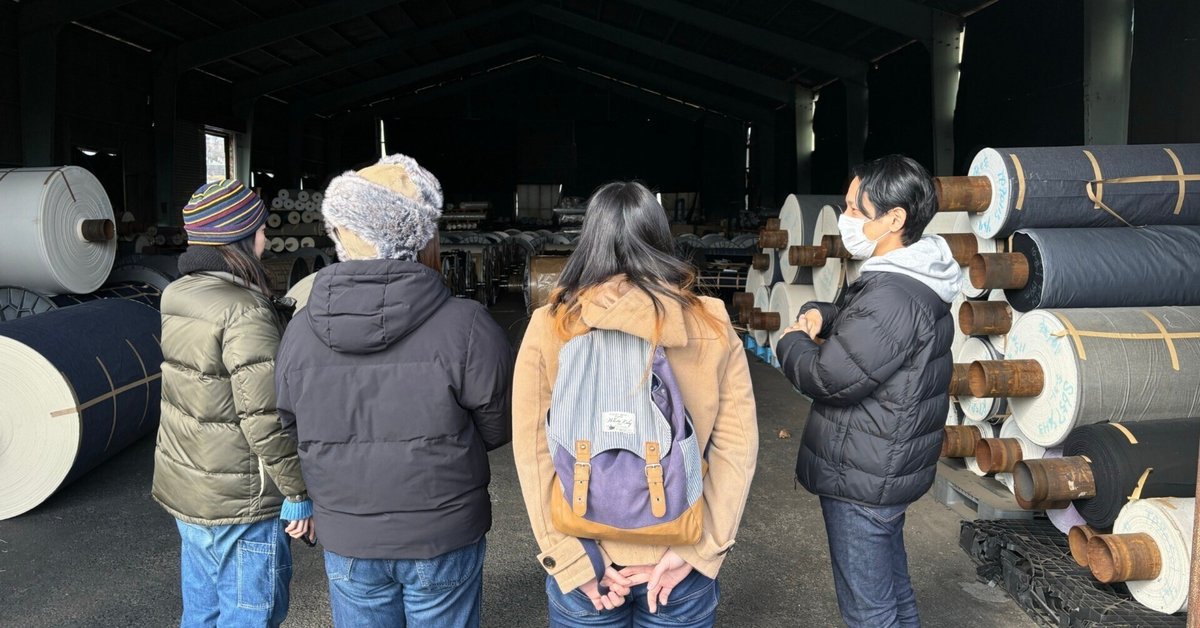
全国にはたくさんのものづくりの産業が存在しており、この地域で連綿と継がれてきたものづくりや、そこで働く人の魅力を伝えたい。そんな想いをもとに、産地から発信する新たなプロジェクトとして「REKROW with WORKERS 100 PROJECT」は始動しました。
農業、鉄工業、繊維業、木工など、さまざまなものづくりの現場で“働く人=WORKER”が、1着のワークウェアを着て1年が経った時、どのような変化が生じるのか。今回のプロジェクトでは、一人ひとりの想いや気持ちの変化をワークウェアを通じて体験していただきたいと考えています。
PJ参加者とデニム産地を巡る
突然ですが、皆さんは普段の生活の中で身につけているワークウェアが、どこで誰の手によってどんな風に作られたものなのか、一度でも考えたことはありますでしょうか。
今回のプロジェクトで私たちが大切にしたいのは、「全国にはたくさんのものづくりの産業が存在しており、ものづくりや働く人の魅力を伝えたい」という想い。1着のワークウェアをお渡しするプロジェクト参加者の皆さんには、そのワークウェアが、どんな場所で、どんな人たちの手によって作られたものなのかを知っていただくことから、プロジェクトをスタートしました。
そこで、PJ参加者の皆さんをお招きして、REKROWのワークウェアの生産工程を含むデニム産地を巡りました。今回はそのツアーの様子をご紹介します!
デニム産地とは ~広島県福山市~
現在、広島県東部に位置する福山市は、デニム生産量は国内シェア約8割を占めていると言われています。この地域の特徴として、紡績、染色、織布、加工、縫製、洗い加工といったデニム製品の生産に携わるすべての工程が揃い、今なおデニム製造関連の企業が集積している国内でもめずらしいデニム産地の一つです。
REKROWがプロジェクト参加者に提供しているワークウェアは、パターン、縫製など細部までこだわり、国内生産によるプロダクト開発を行っています。素材は福山を代表するデニムを使用し、備後地域で縫製・仕上げまで行っているので、まさにメイドインビンゴのワークウェアです!
__________________________________
1.デニム生地を織る|篠原テキスタイル株式会社
まず訪れたのは「篠原テキスタイル」さんです。
デニム産地を巡る上では欠かせない生地メーカーの1社であり、日頃から工場見学等の情報発信や産地間・異業種を繋ぐ取組を行っている企業さんです。
最初に、参加者の皆さんへ、綿(コットン)が1束ずつ渡され、短くてバラバラな綿の繊維の方向をそろえつつ、引き延ばしながら撚りを加えて糸にするという(紡績)体験から座学が始まります。これがデニムの素材です。
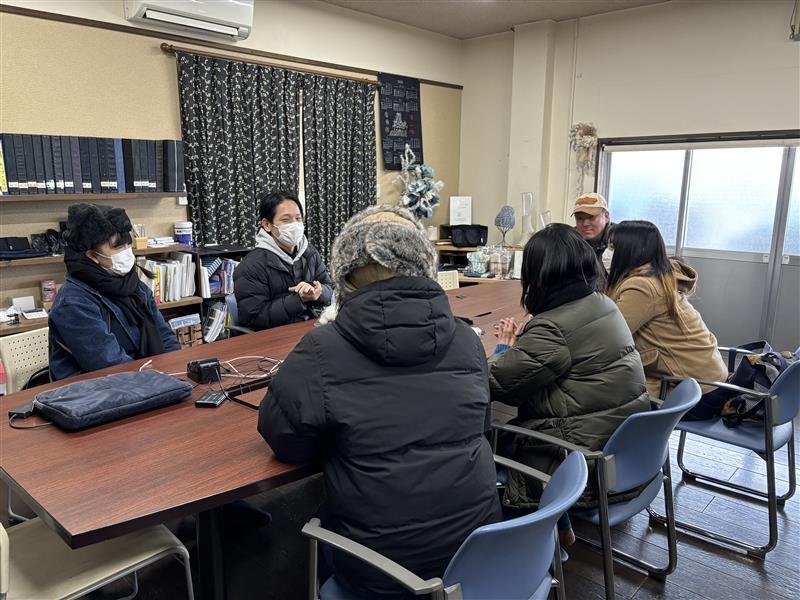
そして、デニムの最大の特徴でもある色落ちする理由について学びました。実際に「インディゴ染料」で
染色された糸の断面を見せていただきました。
糸の中心は染まっておらず、「芯白」になっているのが分かりますね。
これがデニムやジーンズが色落ちをする仕組みになります。
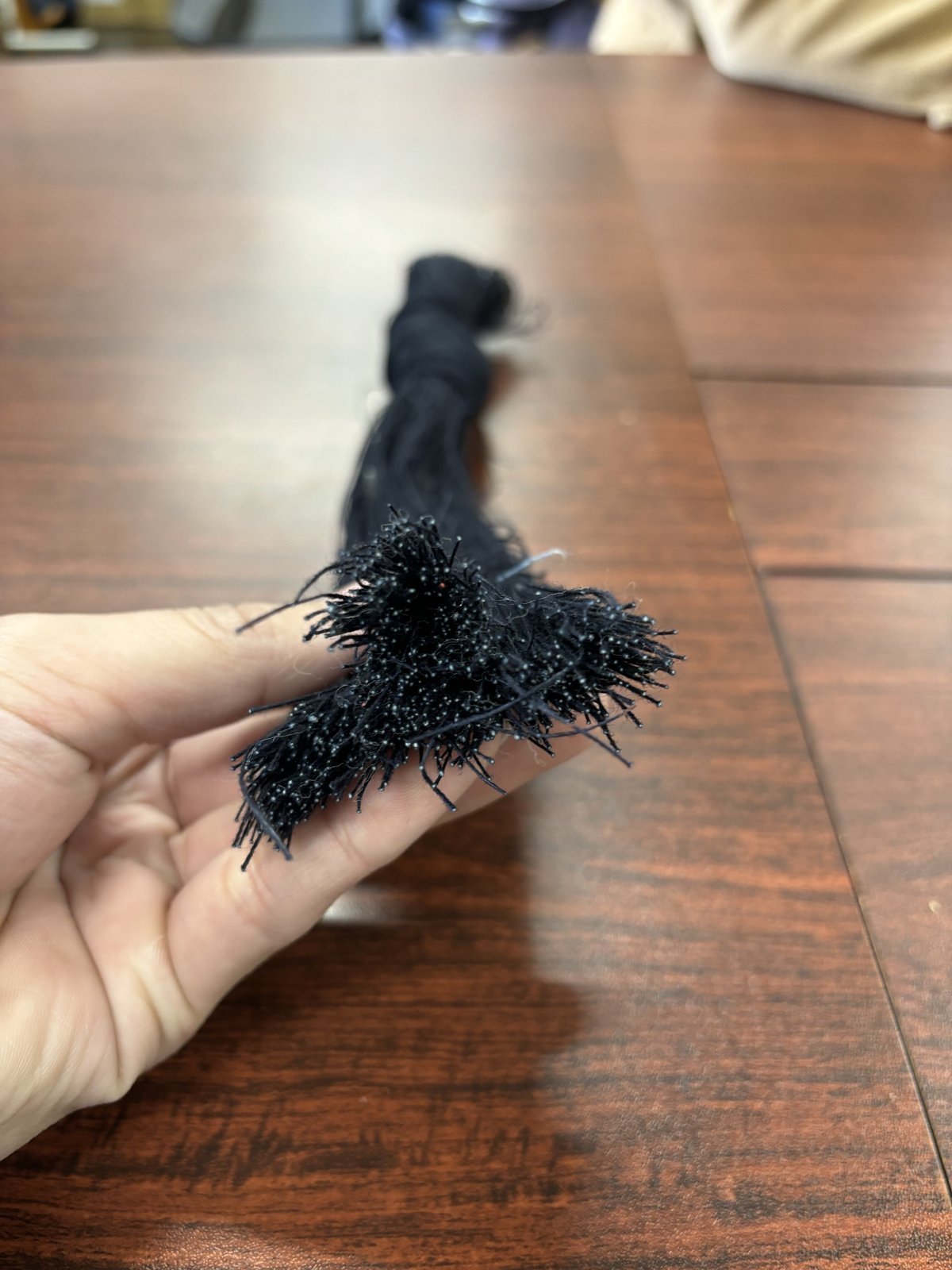
ここから染色された経糸(たていと)と染色されていない緯糸(よこいと)を織機で織り上げるようですが、
デニムの多くは3本の経糸に対して、1本の緯糸が打ち込まれる綾織(あやおり)という織物なのだとか。
こうした説明も実際の生地を見ながら説明していただきました。
綿から糸に、糸から生地になる過程を丁寧に説明していただいたことで、工場内の見学における解像度もかなり上がりました。
エアジェット織機やシャットル織機など、実際に稼働している工場内を見学させていただける貴重な機会は、何度訪れてもワクワクしてしまいます。
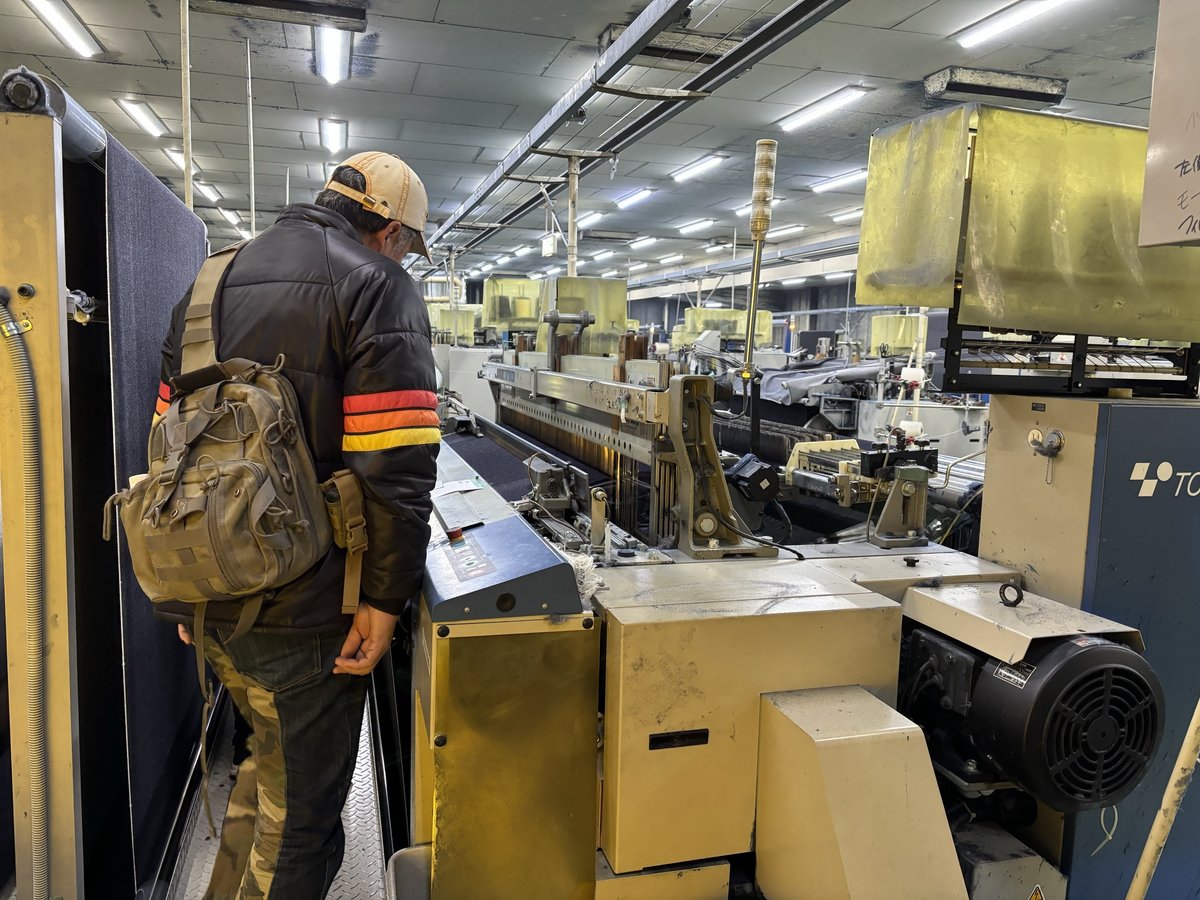
篠原テキスタイル株式会社
広島県福山市駅家町中島703
https://www.shinotex.jp/
_____________________________
2.デニム生地の断裁 | 株式会社サンシャイン
続いて、訪問したのは「サンシャイン」さんです。
ここでは、製品に必要なパーツをできるだけ無駄が出ないように生地から切り出す裁断の現場を見学させていただきました。
1本のジーンズを作り出すのに必要なパーツは約20個ほどと言われており、客先から共有を受けたパターン(型紙)を
指示に従ってチェック・修正を行い、正確に裁断する必要があります。
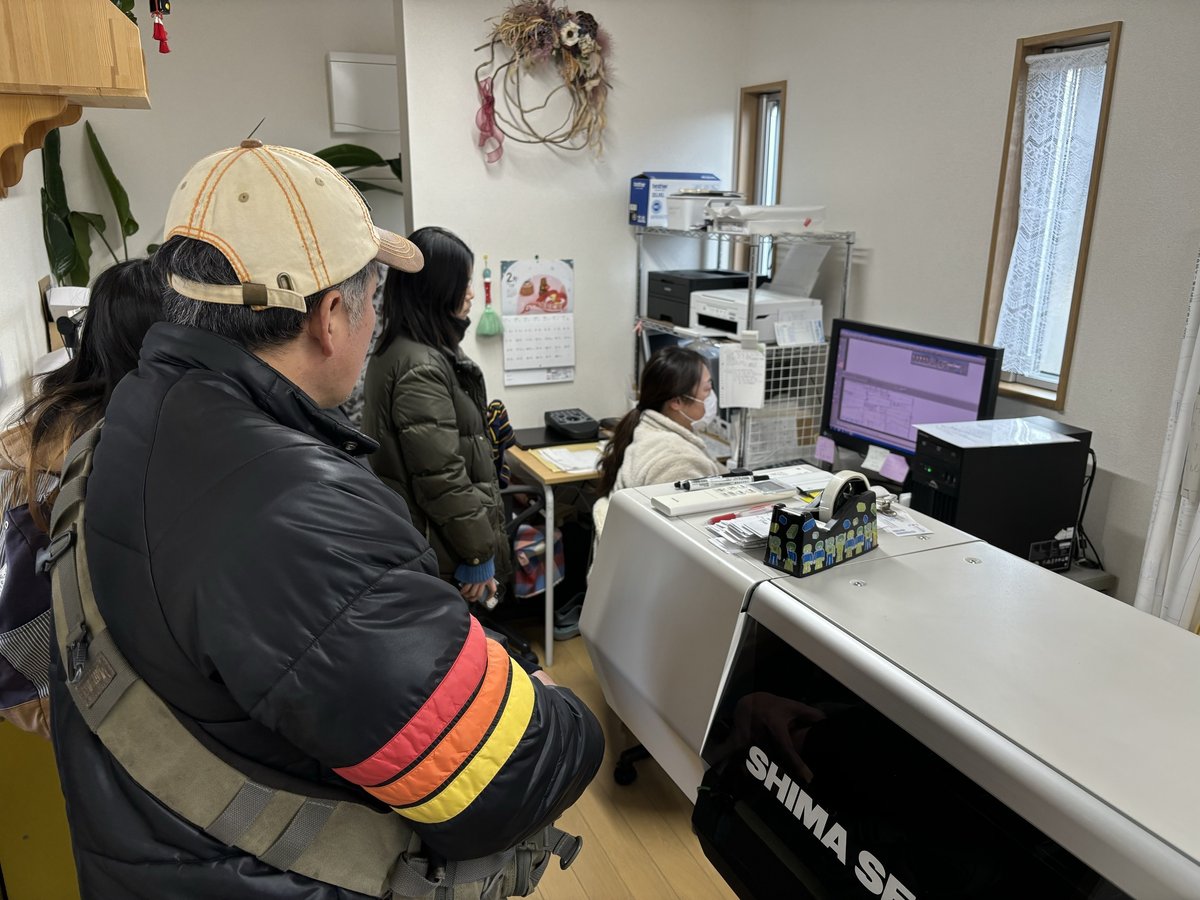
近年では、CAD(キャド)と呼ばれるツールを使って設定された配置に沿って、CAM(キャム)という
自動裁断機を用いて一気に切り出していくのが一般的のようです。
一度に複数枚の生地を裁断することができるようで、あっという間に設定した範囲の裁断が終わっていきます。

最後に、実際に裁断する様子を見せていただきました。
機械がなかった時代は一パーツずつ人の手で裁断をしていたと思うと、気が遠くなるような作業だなと思いつつ、
一つひとつの細かい裁断が後の縫製工場の方々の負担軽減や縫いやすさに繋がっていることを学びました。
1本の製品が仕上がるまでに本当にたくさんの方が関わっている事が分かりますね。
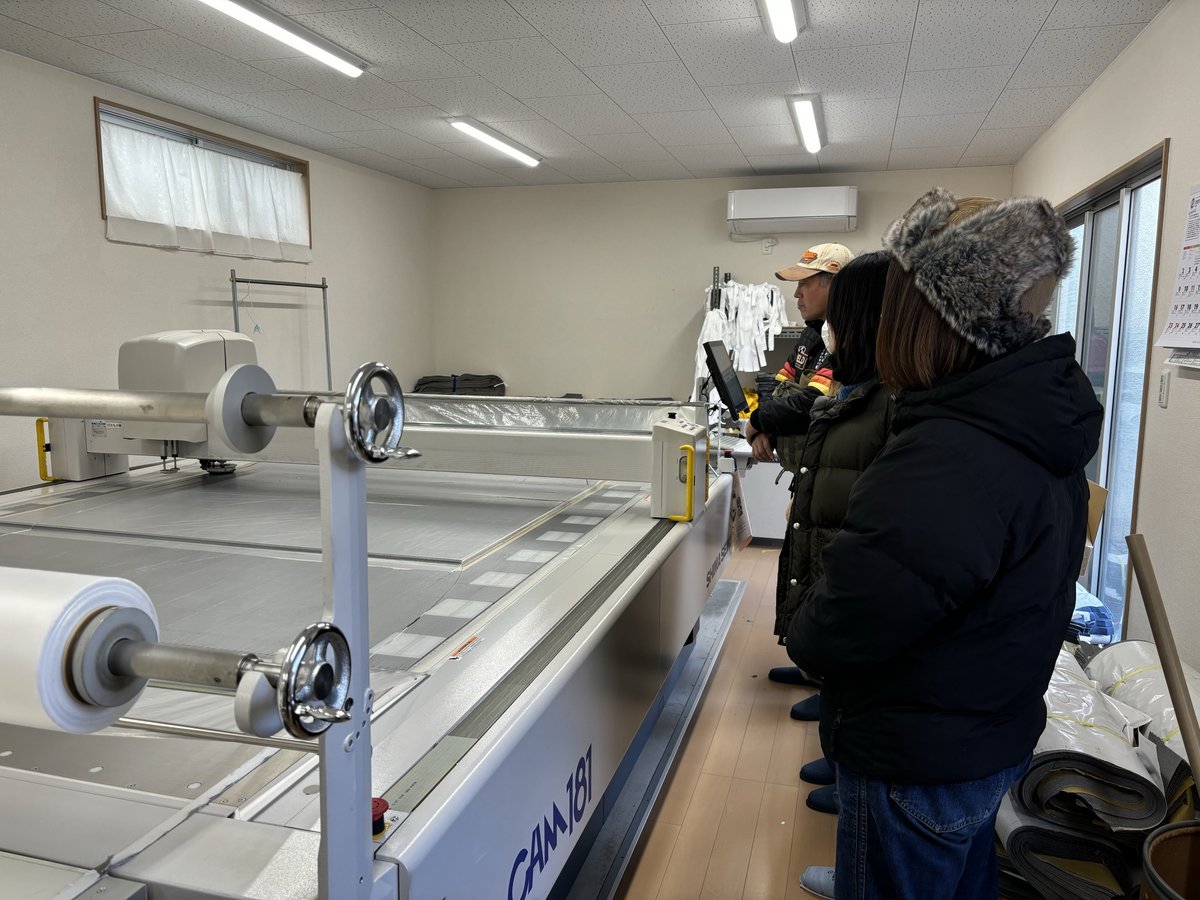
_______________________
3.縫製 | 株式会社エヌ・ディ・エス
続いて「株式会社エヌ・ディ・エス」さんを訪問。
1967年に創立した、国内、海外の有名ブランドのカジュアルウェアから小物類まで製造を手掛ける歴史ある企業さんです。
ここでは、裁断の工程を経て正確に切り出された各パーツを縫製していく現場を見学させていただきました。
1つの製品が完成するまでに、多くのパーツが存在し、工程によってさまざまな種類のミシンが必要になるため、流れ作業で行うのが一般的だそう。
100台を優に超えるミシン所有台数は圧巻で、デニム産地の中でもここまでの台数が揃っているのは珍しいようです。
中山社長のお話の節々から従業員への配慮や繊維産地の存続を危惧する熱い想いを感じることができる時間でした。
株式会社エヌ・ディ・エス
広島県福山市駅家町倉光409
https://nds1967.com/
________________________
4.洗い加工 | 株式会社四川(しかわ)
最後に訪れたのは、株式会社四川さん。
デニムをはじめとする繊維製品の洗い加工や擦り、染色等、主に縫製後の加工を行っている企業さんです。
ジーンズの歴史の中で、作業服というルーツについては皆さんもどこかで聞いたことがあるのではないでしょうか。
ここでは、そんな作業服だったジーンズが、どうしてファッションとして好まれるようになったのか。
流通していく背景にどんな作り手の苦労があるのかを知ることができました。
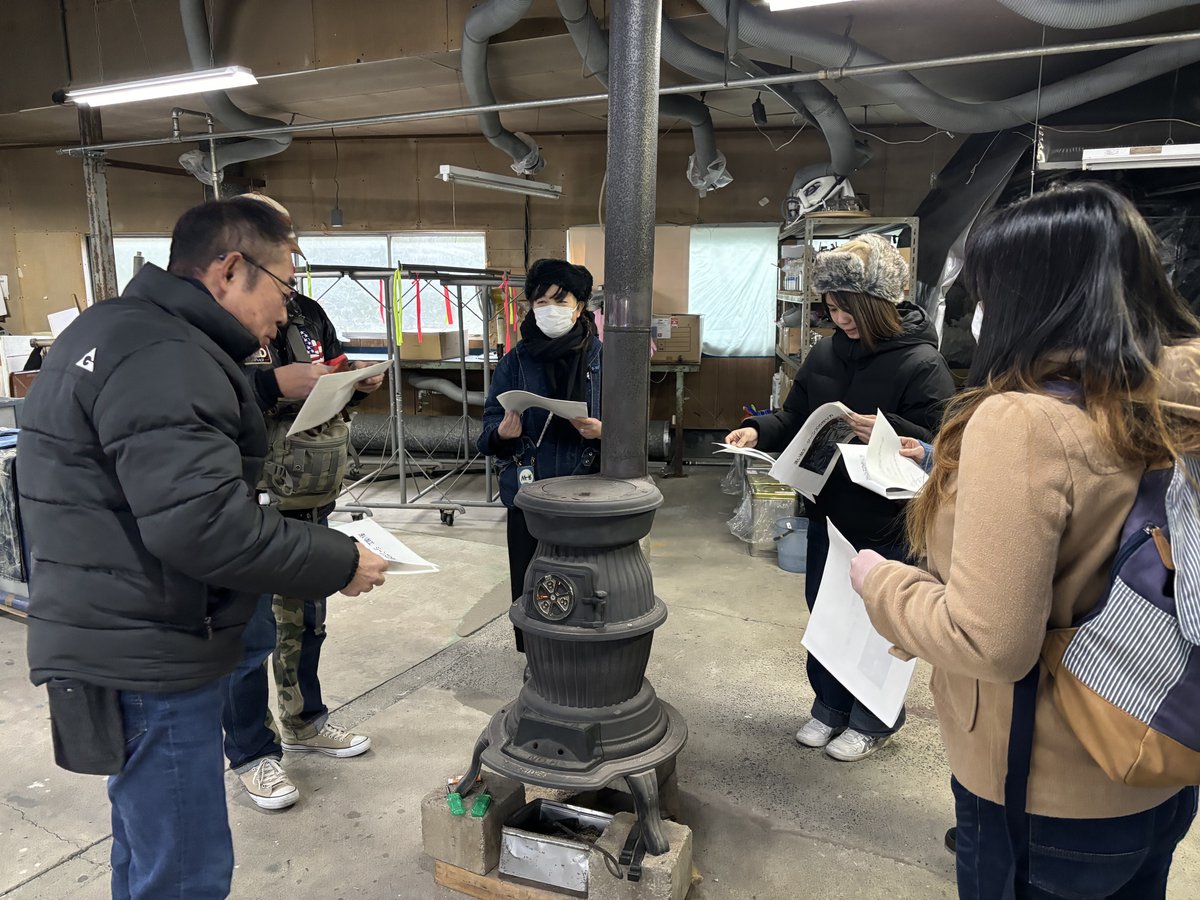
縫製工場で一つ製品の形になったジーンズに職人さんのひと手間が加わることで、履きやすくかっこいいジーンズが仕上がります。
特殊な型を使用してジーンズにアタリを付けていくことで、ヴィンテージ風の仕上がりが実現していることを学びました。
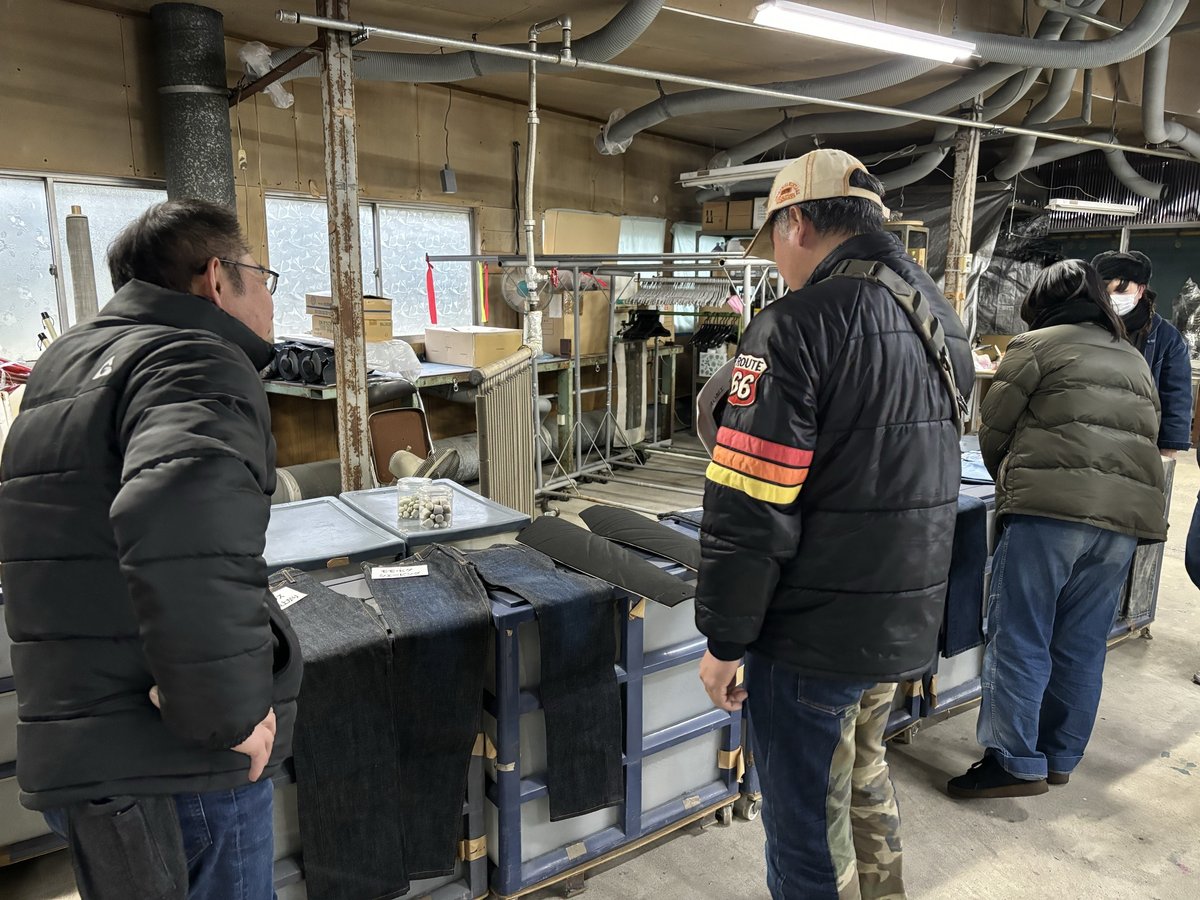
そして、天然軽石や人工石を使用してアタリ感を表現するストーンウォッシュや酸化剤などを用いて脱色をするブリーチなどの技術を凝らして、最初から履きやすいジーンズが皆さんの元へ提供されているのです。
最近では、環境配慮という視点はデニム産地でも避けては通れない課題のようで、薬品や大量の排水処理などにも気を配りながら、人にも地球にも優しいモノづくりを支えてくださっています。
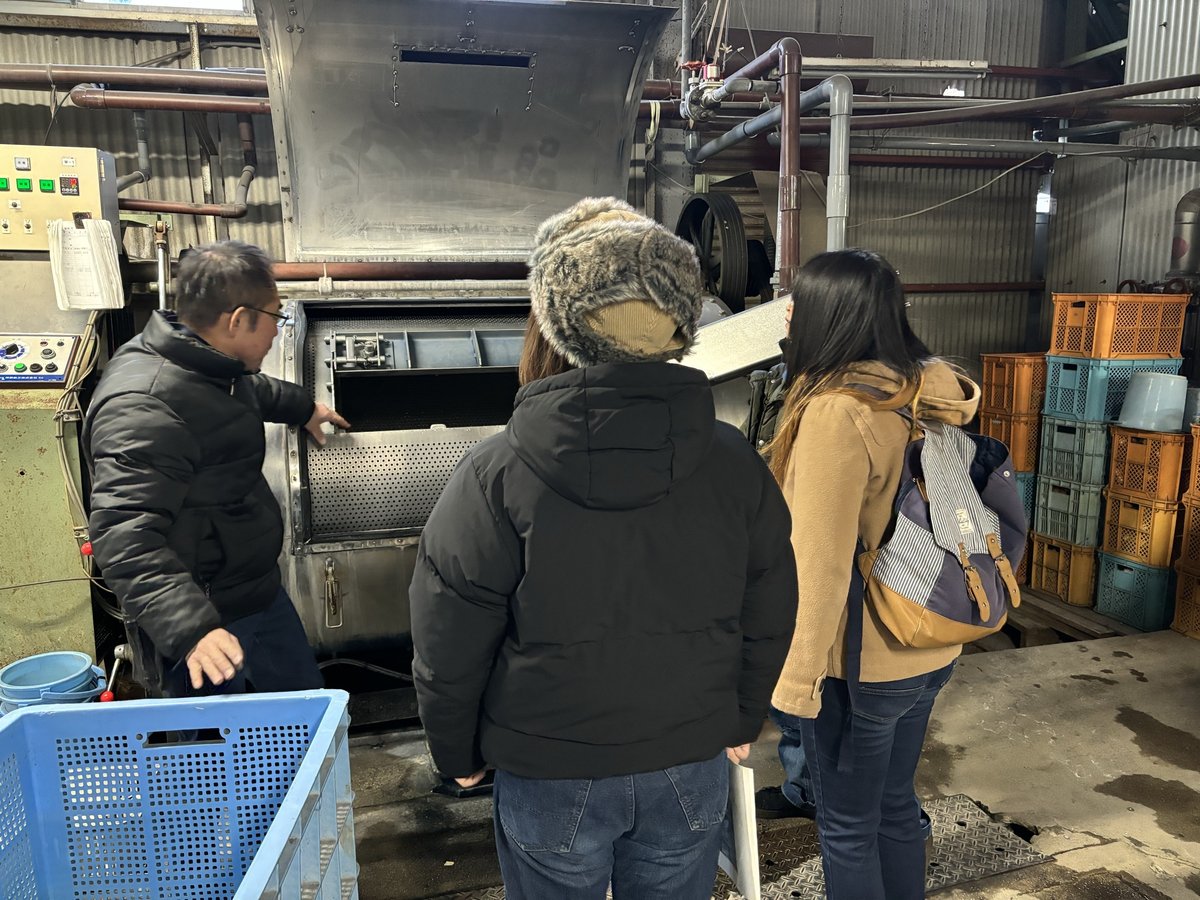
株式会社四川
広島県福山市加茂町字粟根121-2
https://www.shikawa.com/
綿から糸、糸から生地、生地からパーツ、パーツから製品、と多くの方々が繋いできたデニム産地におけるものづくりは、最後の仕上げまで丁寧に行われています。
参加者の方々からは、「こんなに多くの方々か関わっているとは思っていなかった」、「ブランドストーリーだけじゃない、作り手の想いを知ることができて良かった」、「長くモノを使うことにチャレンジしたい」という声が寄せられました。
REKROWとして、ものづくりや働く人の魅力を伝えていくためには、まずは普段から身につけているワークウェアについて知ってもらうことが一番大切だと感じています。
参加者の皆さん、本当にありがとうございました!
selected
使うものを、知り選択する
realized
産地をたずね、身につける
repair
直し、長く使う
これらの想いを持ち「1年」という時間の中で、WORKERの魅力を追求していきます!
プロジェクトの様子は、@rekrow_hiroshima のアカウントで発信するとともに、インタビュー記事などについてはnoteにて公開させていただきます。
皆さまと一緒にプロジェクトを盛り上げていきたいと思います。
どうぞよろしくお願いいたします!
(筆者:元廣 京哉)
REKROW
Instagram @rekrow_hiroshima @rekrow_100pj
note https://note.com/rekrow_hiroshima
Online store https://rekrow-hiroshima.myshopify.com/